Westar Manufacturing Encyclopedia

CNC Machining
OVERVIEW
CNC machining is the process by which material is removed from a work piece with Computer Numerical Control (CNC) equipment that cuts away-unwanted material. Parts are machined from 3D CAD models, processed by the computer and manufactured using the CNC machine.
ADVANTAGES
- Speed – CNC machines can quickly produce parts that would normally take multiple steps to manufacture.
- Efficiency – most CNC machines have an internal quality assurance detector that instantly notifies the operator and pauses production the minute an error occurs.
- Cost Savings – waste is decreased because the operator can optimize raw material usage.
- Flexibility – once a program has been verified and executed for one production, it can be easily recalled for the next run, as well as provide fast change-overs.
- Automation – many CNC machines can run unattended during the entire machining cycle, freeing the operator to do other tasks
TOLERANCES
- In the inch mode, the smallest increment is usually 0.0001 inch. In the metric mode, the smallest increment is 0.001 millimeter
- CNC machining is best used when there is a tight tolerance (+/- 0.005")
FINISHES
- There are multiple secondary options for finishing, including polishing, powder coating, anodizing and many more.
Investment Casting
OVERVIEW
When determining the type of investment casting to use, you must first determine the final purpose of the product. Some of the types include: stainless steel casting, aluminum alloy casting, carbon steel casting, brass and bronze casting, lost wax casting, cobalt casting, tool steel casting, metal casting and rapid prototype casting.
The investment casting process begins by producing a heat disposable pattern. This is accomplished by injecting wax or plastic into a metal die. A pattern must be molded for every casting. The patterns are assembled into a cluster (or tree) and are then coated with various liquid ceramic refractories to form a ceramic shell. The wax or plastic is then melted out of the ceramic shell.
Any number of different alloys can be cast into the ceramic mold. After cooling, the ceramic shell is removed and the castings are cleaned.
ADVANTAGES
- Excellent surface finish
- High dimensional accuracy
- Extremely intricate parts are castable
- Almost any metal can be cast
- No flash or parting lines
TOLERANCES
- A casting process typically maintains dimensional accuracy of +/-.005" per inch, with a surface finish of 125 RMS or better.
FINISHES
- There are many finishing options once the casting is complete. Treatments that can be applied to investment castings include everything from rust protection (with carbon and low alloy steels) to complex corrosion enhancing polishing and painting treatments.
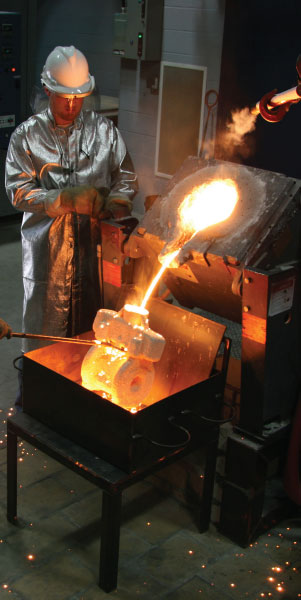